NLIGHT is a vertically-integrated supplier of high-performance lasers that enable innovation in a wide range of technology, defense, and medical applications. nLIGHT develops and manufactures direct diode and fiber lasers based on industry-leading semiconductor laser and optical fiber technology, and often uses Zemax Opticstudio™ software to create breakthroughs in design and development.
Recently, nLIGHT used OpticStudio to work on an important and complex project that could change the quality of the displays we interact with every day. The specifications requested by their customer challenged the limits of laser technology, but nLIGHT—always dedicated to advancement—rose to the challenge.
Using our software, nLIGHT engineers—over the course of a year!—were able to develop a precision multi-kilowatt laser system that will be used to bring about a new generation of smartphone screen/display resolution. This will enable people to have a better experience with the phones and tablets they use every day, especially with photos and video.
We caught up with Principal Engineer Scott Karlsen, the technical lead on this project, to talk about the fascinating potentials of lasers and how they work; what made this project special; and how OpticStudio® by Zemax made it possible to create the next generation of display resolution.
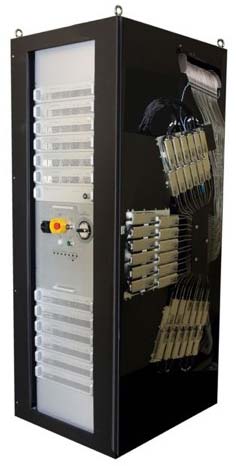
Zemax: How did this project differ from your main laser products? What made it special?
nLIGHT: Our core technology is semiconductor diode lasers—semiconductor chips that emit light instead of electrons. Our core products are diode lasers and fiber lasers, both of which are based on these semiconductor diode lasers.
The most common use for diode lasers is in cd and dvd players. There are millions of those around, and they’re at a milliwatt level of power. Our diode lasers are much higher power, up to 15 watts per laser chip. We then combine many laser chips into packages that produce from tens of watts to many kilowatts.
Most applications require some form of optical system to deliver and manipulate the light from the laser source to the application work surface. Many optical delivery systems are relatively straightforward, and in those cases our customers can take care of the optical design themselves. Occasionally, very complex optical design is required that goes beyond the expertise of most customers, and that is when I get involved.
Zemax: What kind of products use high-power laser diodes?
nLIGHT: They're usually used for pumping energy into other kinds of lasers, like fiber lasers or solid state lasers based on a crystal. These lasers have higher beam quality that can be focused to smaller spots and stay collimated—that is, the same beam size for longer distances. They are used for processing materials, like marking or cutting metal. They also get used in surgical equipment, industrial processes, engraving logos and letters onto parts. A laser with good beam quality allows high precision.
Zemax: But this project was not related to that?
nLIGHT: Right. In this case, our customer is a display manufacturer. They make TV screens, as well as cell phone and tablet displays. And they’re constantly researching ways to make higher resolution displays. I can’t say the name of the customer for confidentiality reasons—but it’s a big company; people would recognize the name.
The company had an idea for a way to create higher resolution displays. It involved using a high-power line of light—that’s the part we provide—to deliver the energy for a thermal process. A laser can provide enough energy to create a thermal reaction, but you need lots of power. They needed this power over a wide area, as the line of light has to be larger than the size of the screen they’re processing.
To accomplish their application, the customer required a line longer than 200mm and narrower than 200 microns with greater than 7,000 watts of power to achieve the optical density on the work surface. In addition, the line of light had to have ultra-high uniformity.
I like to tell people to think about a 100-watt light bulb and how hot it would feel if it had been on for a while and you grabbed it. Now imagine you put that heat into something the size of a human hair. That’s the perfect analogy for what we’re doing here. We’re putting 7,000 watts of power into an ultra-narrow line of light.
That’s why lasers are so ideal for high-precision processing. They can channel a lot of energy into an extremely small spot or area, and it can get hot enough to melt metal—like 2,000 degrees Fahrenheit.
Think about a 100-watt light bulb and how hot it would feel if it had been on for a while and you grabbed it. Imagine putting that heat into something the size of a human hair. That’s the perfect analogy for what we’re doing here—putting 7,000 watts of power into an ultra-narrow line of light.
Zemax: And you were able to get 7,000 watts of power into a such a long, narrow line of light with ultra-high uniformity?
nLIGHT: Although it was an extremely challenging project, yes—we were able to do it. Our approach was to combine 72 of our 100-watt diode laser modules into a single beam of light shaped into a line with an initial optical module. Then we used a second optical module to homogenize the light to achieve the ultra-high uniformity. Finally, we used a third optical module to image the homogenized line beam onto the work surface.
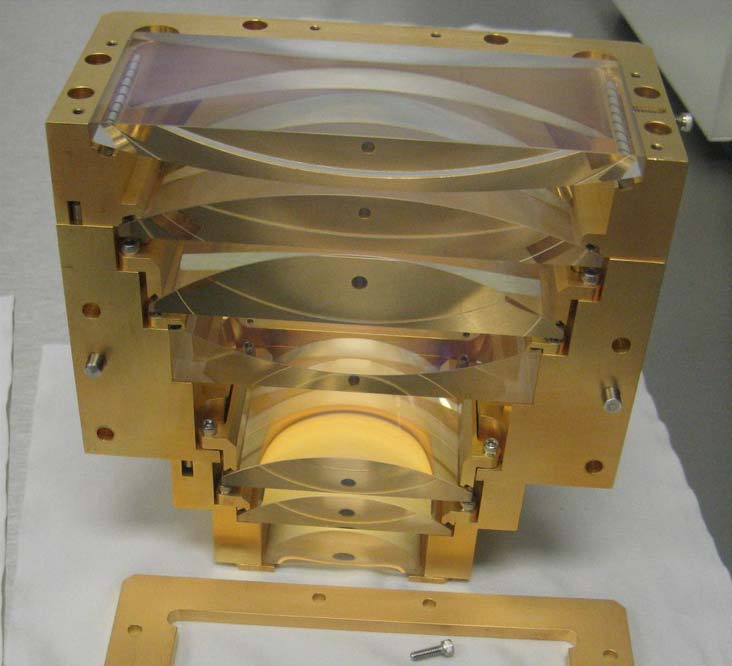
And designing imaging systems is a key sweet spot for OpticStudio. The sequential ray tracing feature is key for this. People have been using ray tracing software—Zemax’s in particular—for a long time to design really good imaging systems. OpticStudio’s ray tracing functionality is leading-edge.
Our imaging system was unusual in that it was made out of all cylinder lenses because of this high aspect ratio line—very long by very narrow. There are subtleties involved in designing with cylinder lenses that don’t appear with systems that use spherical lenses.
Zemax: So did you use OpticStudio to design lenses too? nLIGHT: Yes, for the imaging part of the system, we made a couple of different lens assemblies. Very high-tolerance lens design of individual lens components was critical for us in making sure this whole project met all specs the first time around.
The next challenging part was that it had to be extremely mechanically stable. We needed to process extremely small pixels on a screen, so this laser needed to operate not only at very high power, but also with incredible mechanical stability. It couldn’t move more than 10 micrometers. For reference here, a human hair is 50 to 100 micrometers.
Zemax: So, basically almost no movement.
nLIGHT: Right. The software played a big role in that too: to control that movement, you have to control the heat and the stray light. We had 7,000 watts going through this system, and every optical surface, every lens reflects a little bit of light. That lights goes somewhere and heats up some mechanical part. When something heats up it thermally expands, and thermal expansion leads to movement.
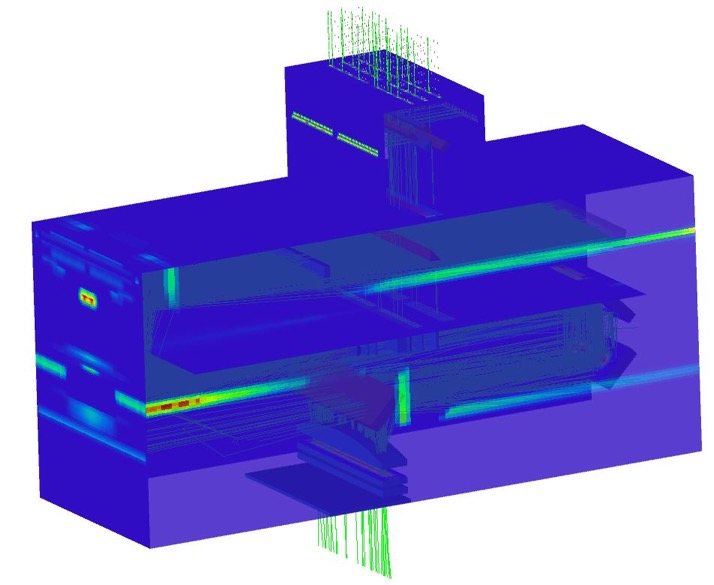
Again, OpticStudio has non-sequential ray tracing capability. We took advantage of that and did a stray light analysis of the entire system, including all mechanical and optical parts, assessing how much reflection each surface would produce. With this modeling, we figured out what parts would get warm, and that enabled us to take steps to control that heat—adding water-cooling or air-cooling capability. Some parts we plated with gold—gold reflects light and stops it from absorbing.
We also used the non-sequential capability in designing the homogenizing system. It worked really well. Once we combined the 72 beams, those were launched into what’s called a light pipe—that’s the kind of homogenizer we chose to use. A lightpipe is a glass rod. Or in our case, really, a flat glass plate, where the light is bouncing back and forth between the parallel sides of the plate. If we make the plate long enough and get enough bounces, what comes out the end has to have constant intensity—this is a way of smoothing out the variation in power across the beam.
Zemax: How many of these systems were there? Did you build a series of these in order to get it right? Or just one?
nLIGHT: We built a prototype first, but it was a situation where the customer had a very hard deadline, only one design cycle to make it work. Therefore, we had to carefully model everything: optical design with potential optical manufacturing tolerances and stray light analysis, as well as the full mechanical design with thermal analysis.
Zemax: So what exactly did you end up delivering? How can we picture this?
nLIGHT: The end product we delivered to the customer was called a laser line generator. It consisted of an optical head for converting the 72 individual lasers into a single laser line, and an electronics control rack. The optical head was about four feet long, two feet wide and two feet high. The control rack is about the size of a refrigerator, and it houses 72 100-watt laser modules, a cooling system, power supplies, and control electronics.
We were working with multi-kilowatt laser beams that are powerful enough to cut metal—yet we couldn't see them.
Zemax: What kind of environment do you have to be in to play with lasers that intense?
nLIGHT: This laser was built in a Class 1000 clean room—which is what most of our facility is. Because of the high power output, you want to keep all the surfaces as clean as possible—no dust. Dust can cause burns that will damage the lenses.
Also, our lasers operate at a wavelength that is invisible to the eye. We were working with multi-kilowatt laser beams that are powerful enough to cut metal, so they represent a very serious safety hazard—yet we couldn't see them. Just the stray light from one of these beams is enough to blind a person if they looked at an object that was being hit by the beam, such as the power meter.
There are standard safety practices that enable safe operation of high-power lasers, including the use of special laser safety goggles that block any laser light from getting in our eyes. We use cameras similar to a night vision system to see where the beam is going. We also use precautions like guards that prevent people from putting their hands in the beam.
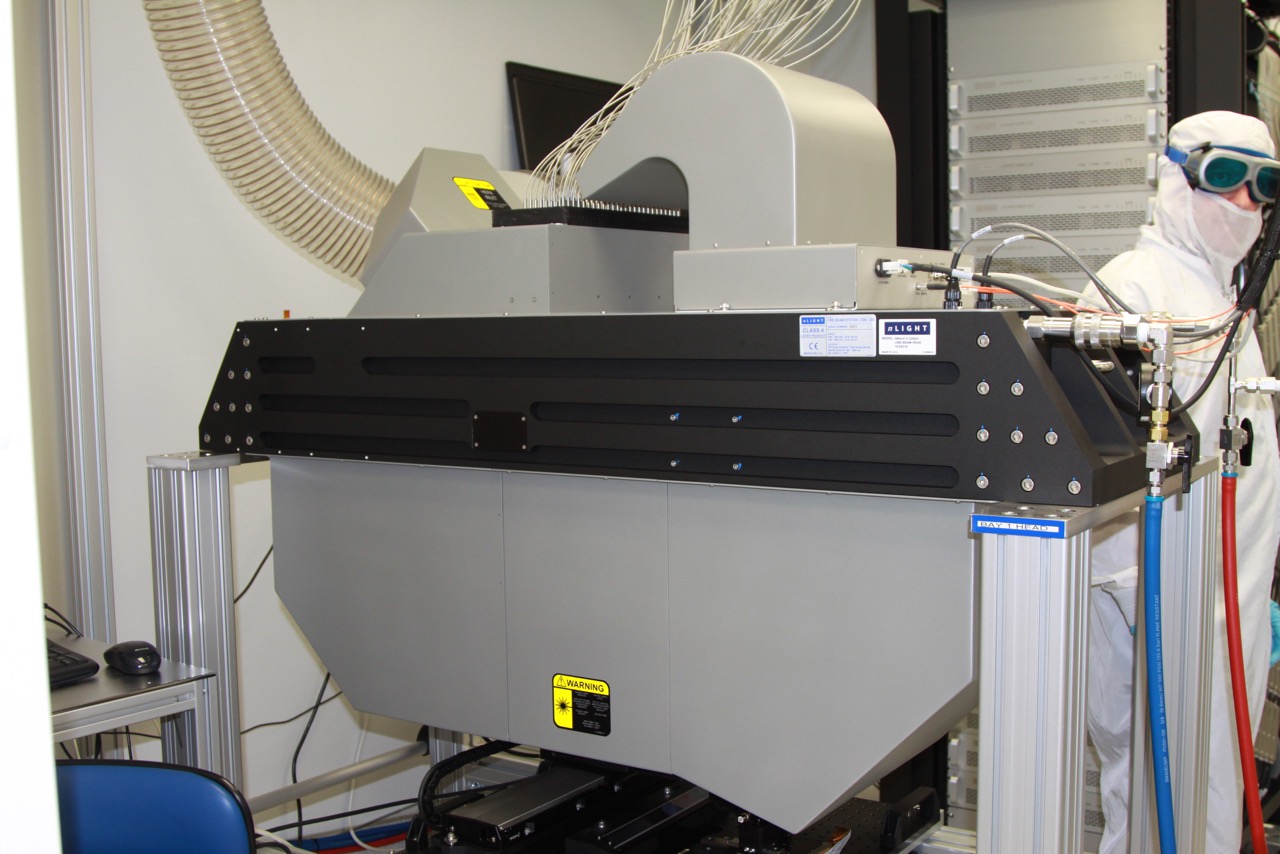
Zemax: How long did it take you to build this laser?
nLIGHT: With a project like this, you’re looking at nine to 12 months. The design work is very intensive and can take up to three or four months on these kinds of very complex systems. In the procurement cycle, procuring large custom lenses always requires a long lead-time, and they can take up to three to four months for fabrication. Then we need a couple of months to put the system together and debug it.
Zemax: How will this line generator get used? Will it be used to prototype something before manufacturing, or used on every screen that gets made?
nLIGHT: Yes, it will get used on every screen. Most likely each screen would be scanned underneath the laser during manufacturing. The laser would provide this thermal effect of heating something up to a well-controlled temperature, for a specific amount of time. This heating process was critical to their process of making a higher resolution screen.
Zemax: Are they using it already? What kind of resolution improvements are we looking at as a result of this new laser system?
nLIGHT: The feedback was that it worked great for them. Our line generator enabled a high-resolution process that allowed production of resolutions up to 1000ppi. For comparison, the iPhone 6 has a resolution of 326ppi, and the Galaxy S6 Edge has a resolution of 557ppi.
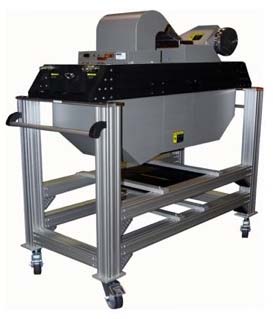
Zemax: What’s the functional difference between 500ppi and 1000ppi?
nLIGHT: This is a really interesting thing. There’s a controversy brewing about the limits of human vision. Does it make sense to have pixels smaller than that limit? You would think not, but as display manufacturers have improved resolution and gotten beyond where people thought that limit was, they find there’s still a better user experience, even if we get beyond where we thought that human vision limit was.
This implies that earlier information we had on human visual acuity is probably not totally accurate, or didn’t take into account subtle effects related to how the brain detects motion really well, especially with things like line steadiness.
With moving pictures, the eye is very sensitive to discriminating movement, especially movement of an edge along a row of pixels. For video and games especially, it seems that the human eye and brain are still better at picking up subtle small effects than we may fully understand.
That means there is still room for improvement in visual experience, and that’s what this company was aspiring to do in their ongoing quest for innovation. And it was pretty exciting to be able to build a laser powerful enough to help them do it.